Appearances are Deceptive
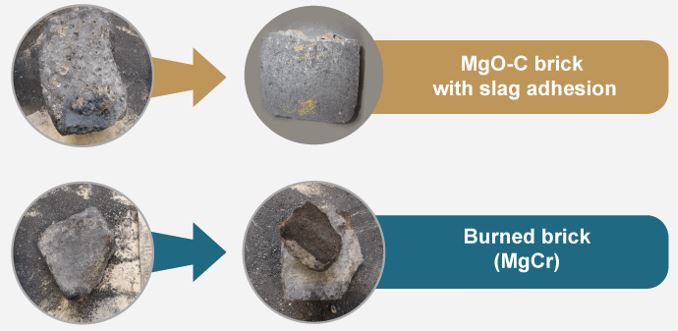
In the last few blogs, we described how we took representative samples of refractory breakout materials from two different industrial aggregates in order to get an overview of the secondary raw materials and to be able to initiate the necessary chemical and mineralogical investigations. As you could see, we put a lot of physical and organisational effort into the sampling, something that is rarely necessary to such a degree in our day-to-day business. Perhaps some of you might have already asked yourselves why we go to such lengths?
The aim of all this preliminary work in a single piece sorting and the subsequent examinations is that we need a large selection of known and examined material for upcoming tasks in the project, as we want to be able to train the new machines/sensors of the automatic sorting system properly.
Each sensor can later only work as well as it has been previously programmed and calibrated by us with known compositions of recycled raw materials. Since every industrial customer has chosen an optimal refractory lining in the different aggregates, considered for his overall process, the variety of refractory material that has to be sorted can be very broad. In addition, the breakout process and intermediate storage are not the same at every customer’s, so that there may also be other materials among the used refractory pieces that are not immediately visible.
Therefore, we photographed every single brick from the representative sampling (approx. 400 kg from a steel ladle or 1000 kg from a cement rotary pipe), determined the approximate dimensions and the residual weight. By cutting off a corner and making the internal material structure visible, we then tried to assign the correct refractory material to each individual sample.
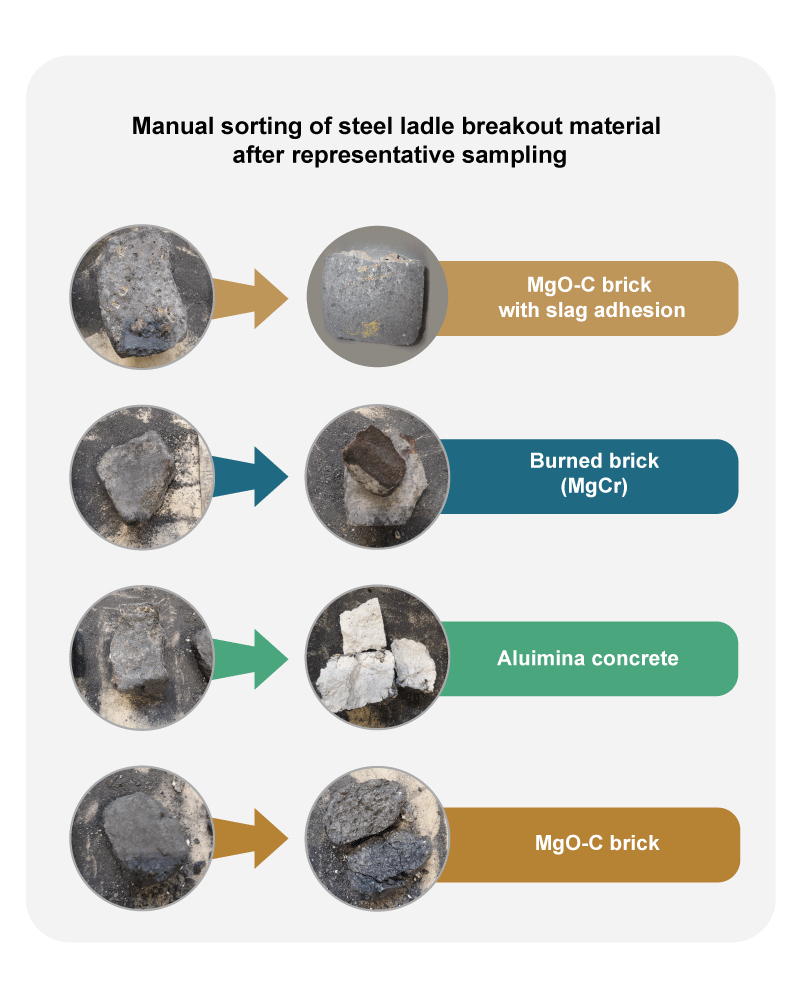
As you can see in the pictures, sometimes the first impression is deceptive and only when you cut deeper into the material, the type of material can be identified correctly.
Normally, we mainly want to recycle the high-quality magnesia carbon bricks (MgO-C) in a steel ladle excavation, because the carbon matrix prevents too much infiltration of slag and steel and the bricks therefore still have an unchanged structure to a large extent.
Since these magnesia carbon bricks have a carbon bond, the brick structure is grey-black. However, due to the mixing of different types of material in a delivery concept of an aggregate at the customer’s site or due to storage or pre-sorting that is not pure by type, other refractory materials may also have found their way into the breakout material of a steel ladle. Another complicating factor is that, due to the processes in the steel plants, all materials can sometimes have a black outer layer and it is only the brick structure that reveals the truth of the material type. An additional difficulty then is the further refractory material combination of the Alumina-Magnesia-Carbon bricks (Al2O3-MgO-C / AMC for short). Here, too, a carbon bond exists and the matrix appears grey-black, but the main raw material is not magnesia (MgO) but corundum or bauxite. And mixing between MgO-C and AMC recycling raw materials is undesirable for reuse. In order to prevent this mixing in the future, the automatic sorting system uses, among other things, the LIBS system from project partner LSA.
The samples selected here will be the first training material for our new sensors at the project partners NEO, Fraunhofer ILT and LSA at a later stage of the project.
Partner
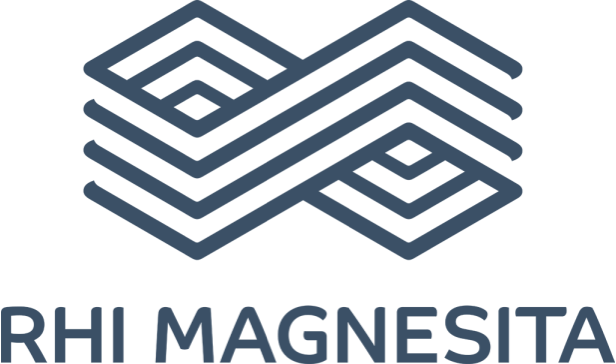