Demonstrator B

ReSoURCE’s main objective is to increase the recycling rate of refractory bricks. Broken-out refractories already have a non-negligible fines content when they are first removed, for example from a steel casting ladle. In further processing, RHI Magnesita crushes them into smaller blocks with a maximum edge length of 120mm, to be sortable by the new equipment. These single grains are sorted with the so-called Demonstrator A, which is also developed and evaluated during the project. The crushed bricks are then screened to minimize dust generation and contamination during the sorting process. In each individual step, fine particles are thus created. During the ReSoURCE project, we speak of fines at grain sizes smaller than 5mm.
Demonstrator B (Demo B), which we consider in this post, is designed to process these fines, and contribute to an enrichment of the desired material classes. Demo B can be seen as a scientific approach to enrichment rather than an industrial facility. Its purpose is to analyze and evaluate the handling and sorting of fine parts in a sorting plant. All modules of the plant are designed in such a way that they can be interchanged in their sequence. This allows the material flow to be tested in different configurations of the plant, to find the optimal setup for a later industrial approach.
In the sketch a first preliminary design of the setup is shown: The fines that are generated during the above-mentioned process steps are collected in a hopper (1). With the help of a pump (2) an air flow is generated which transports the fines through the system. During this process, the fine parts pass-through various stations.
First, the chemical composition of the different grains will be examined as a bulk by a measuring system (3) using Laser-induced breakdown spectroscopy (LIBS) provided by LSA. With LIBS, the chemical composition of a material can be analyzed in a contact-free and non-destructive manner. After analyzing the composition, the sorting of the fines can start. The sorting can be distinguished in two different types of sorting methods, direct sorting (4) and mechanical sorting measurement (5). Direct sorting in this application means, a sorting based on physical or chemical parameters and requires no additional sensor in advance.
Examples for the direct sorting modules could be a vibrating table classifier, that separates smaller from bigger grains by feed them through holes with different sizes. Mechanical sorting method could be implemented by using a mechanical flap, that divides the fines-flow into two different collecting bins, corresponding to the chemical composition. The sorting methods are developed and tested by SINTEF. If you want to learn more about SINTEF’s work, check the blogpost Powder Classification.
The sorted material is finally conveyed into collecting bins and can be processed further by RHI Magnesita.
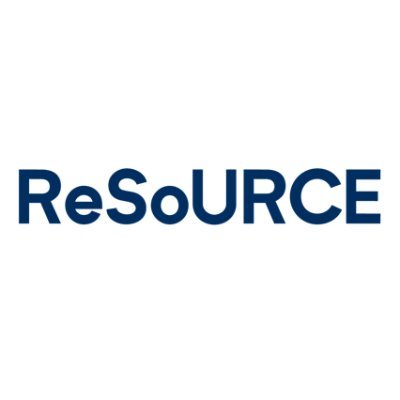
Author’s Portrait
Carsten Coenen
Carsten Coenen is a development engineer at LSA – Laser Analytical Systems & Automation GmbH (Germany). He is working on the mechanical design and the implementation of high-precision 3D-printed parts for use in optical modules. Since 2022 he has been working at LSA. Previously, he completed an apprenticeship as an electronics technician at RWTH Aachen University and received his B.Eng. Mechatronics and M.Sc. Mechatronics from FH Aachen University of Applied Sciences.
During his studies, he already worked as a working student at RWTH Aachen University and at AGVR GmbH (Germany). Since he joined LSA, he has also been involved in EU projects (e.g. REVaMP and ReSoURCE).
Partner
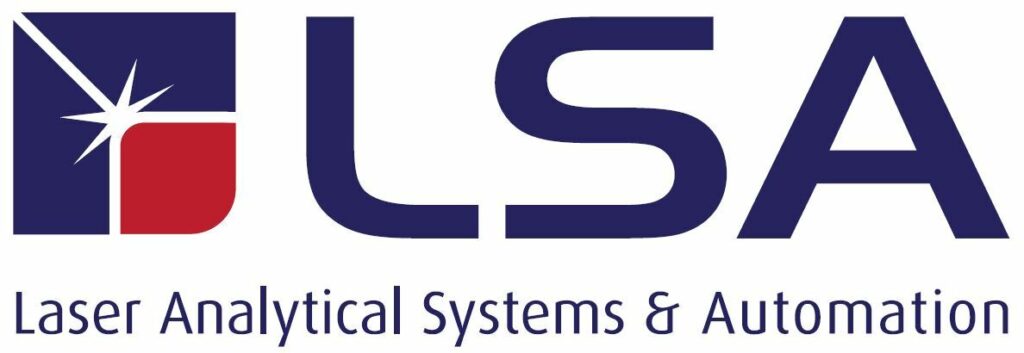