Sort of an Issue – An Interview with our Technical Project Leader Alex Leitner
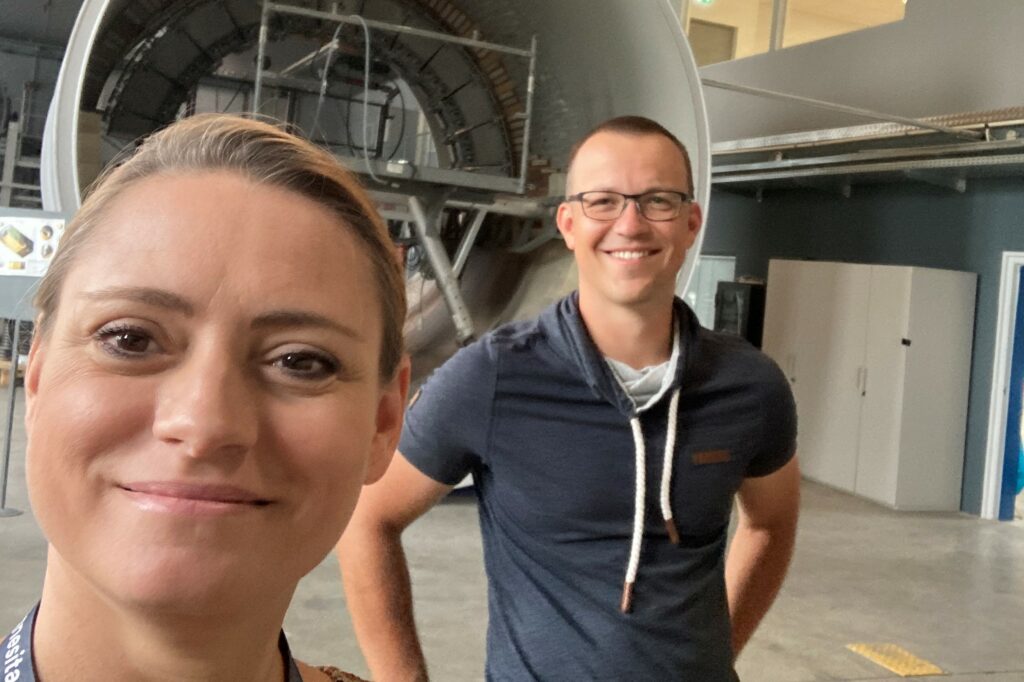
Recently I paid a visit to the RHI Magnesita sites in Leoben, Steiermark. Alexander Leitner (AL), our technical project leader, showed me around and, of course, I used the opportunity to do a brief interview with him.
Carmen Loew (CL), Science Communicator for Project ReSoURCE
CL: Alex, we are here in RHI Magnesita’s Training Centre in Leoben. What exactly happens here usually?
AL: Here RHIM trains clients and internals on how to handle and install the refractory products correctly. In another section of this building, we also have some research facilities.
CL: What kind of products does RHIM sell? Because at first glance, these bricks look like products from the building industry.
AL: Yes, they do. Basically, RHIM produces heat resistant bricks and mixes. The latter is often sent to the clients in form of a dry mix. The clients add water or other liquids and use the material then like concrete. Refractory products come generally in a variety of shapes and forms, but most of all they differentiate regarding their components.
CL: What are the main components of refractory products?
AL: The main components of many refractory products are Alumina, Silica and Magnesia. Magnesia is a mineral phase gained from the raw material Magnesite. RHI Magnesita has some mines in Austria, China, and Brazil. One of our mines for example is in Breitenau, here in Styria. If I am not mistaken, in this mine we are working on almost the deepest point in the territory of Styria.
CL: I’m looking forward to seeing this one day. But let’s go back to the raw material. What is the next step after the mining? How do you gain Magnesia from Magnesite?
AL: If you want to change Magnesium Carbonate (Magnesite) to Magnesium Oxid (Magnesia), you need to drive out the Carbon dioxide. This is done by burning and has therefore an inevitable impact on the environment. Every industry that has a Carbonate as basic raw material faces the same problem: emissions are not just coming from the burning process but already from the raw material itself. There is actually no way out of this if you are working with such a primary raw material.
CL: Is there no alternative in using a different material then?
AL: No. Magnesia is produced for more than 100 years. Before that Alumina and Silica have been used – and are still in use today for some products. But those materials have a much lower melting point. Since our clients – let’s say in the Steel industry – constantly improve their processes they now work with a higher temperature or want a longer lifetime of refractory products. That’s why the use of Magnesia is unavoidable. Only Magnesia has a melting point that is high enough. With around 2800°C it exceeds Alumina with 2100°C and Silica with only 1700°C.
CL: Is there a way to improve the production of Magnesia?
AL: Hardly. There are almost no options left for energy savings. The process is more or less out-optimised. That means, whatever research is done on this end, we will hardly be able to reduce the CO2 emissions to a noteworthy extend.
CL: So, reducing the CO2 emissions is in the case of fire-resistant products not so much a question of energy saving. It is a raw material problem.
AL: Yes. There are options to work with another raw material. For example, one could use Magnesium Hydroxide from sea water, but to do that, you need six times the amount of energy that you need for Magnesite. You can choose now what the greater evil is.
CL: Is that why this recycling project is so important?
AL: Yes, recycling offers an environmentally friendly solution. When you can use a secondary raw material, you don’t have to expel the CO2 from it. That makes a real difference.
CL: Why is that not done already then?
AL: Recycling in the refractory industry is a rather challenging endeavour and that for sure is one of the main reasons why it is still rather in its infancy compared to other industries. In the beginning, it was more or less used to safe some costs but given the climate change it has come in our focus for much different reasons.
CL: Why exactly is it so challenging?
AL: The most challenging aspect is the variety of components in refractory products, as these products always have to be customised. To begin with, one reason for customisation is that different industries need different products. Also, in these industries the clients’ products are different from the ones of their competitors. But even if two clients basically need the same product, there might be different process conditions – like norms for example – hence the spent refractories might be different. RHIM alone produces hundreds of different products. To recycle them after they have been used is therefore far from simple.
CL: So, this is why ReSoURCE is focussing on the sorting then?
AL: Yes, the proper sorting of used refractory material is crucial to produce a recycling material of high quality. Our project’s acronym ReSoURCE stands for Refractory Sorting Using Revolutionizing Classification Equipment. We will develop a new sorting machine with high-end high-tech equipment to make sure that we can sort used refractory material as precise as possible with today’s technical options. If that can be achieved, we will be able to gain a high-quality secondary raw material that can be used without causing a massive carbon footprint.
CL: Thank you for the interview. I’m looking forward to hearing about our researchers’ solutions for these sorting issues.
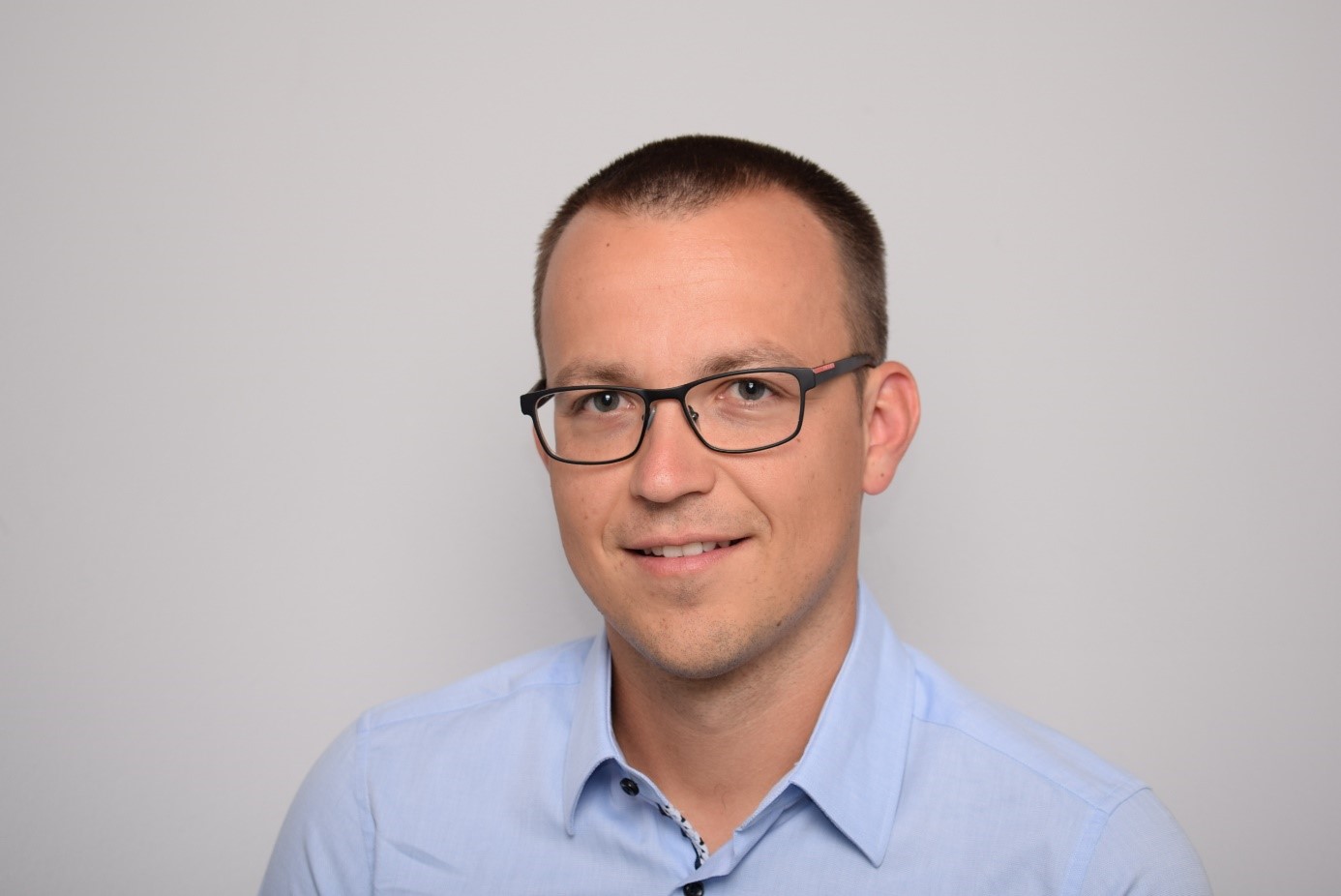
Author’s Portrait
Alexander Leitner
Dr. Alexander Leitner studied Material Science at the MOntanuniveristät Leoben, focussing on the field of micromechanics and material physics. He joined RHI Magnesita’s Strategic Project and Innovation Team in 2019 and recently joined the business unit Recycling in the field of Recycling Innovation and Technology.
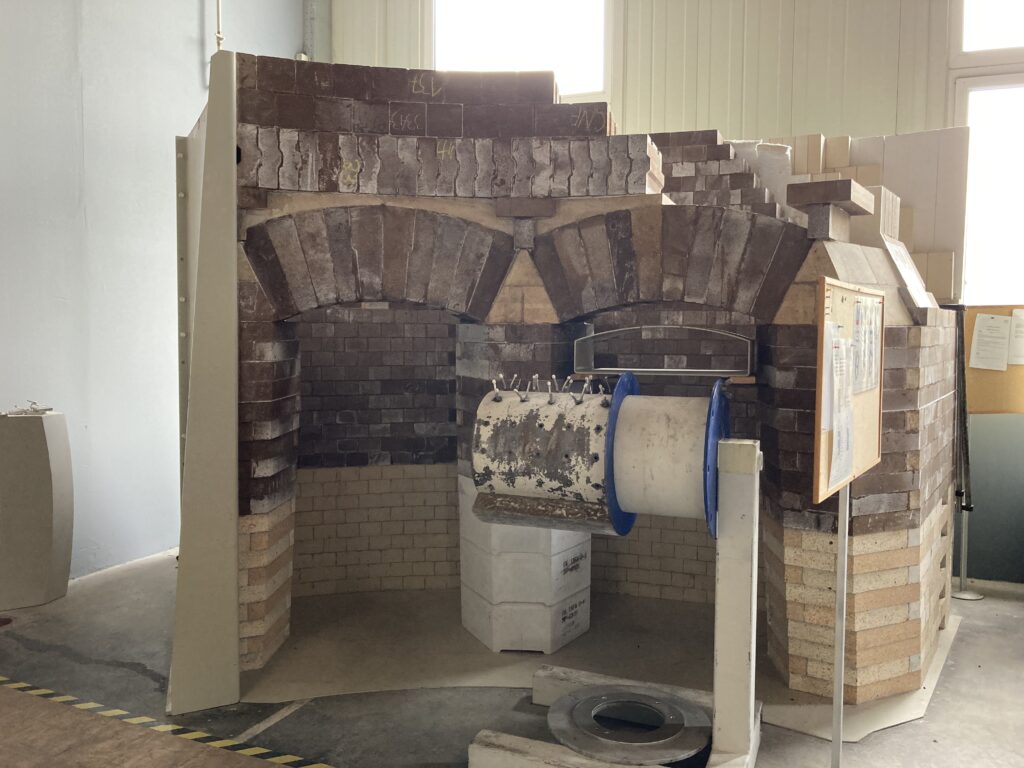
Partner
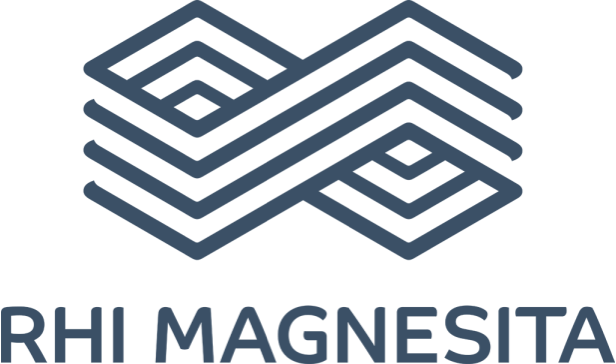