The Development of Our Sorting Plant
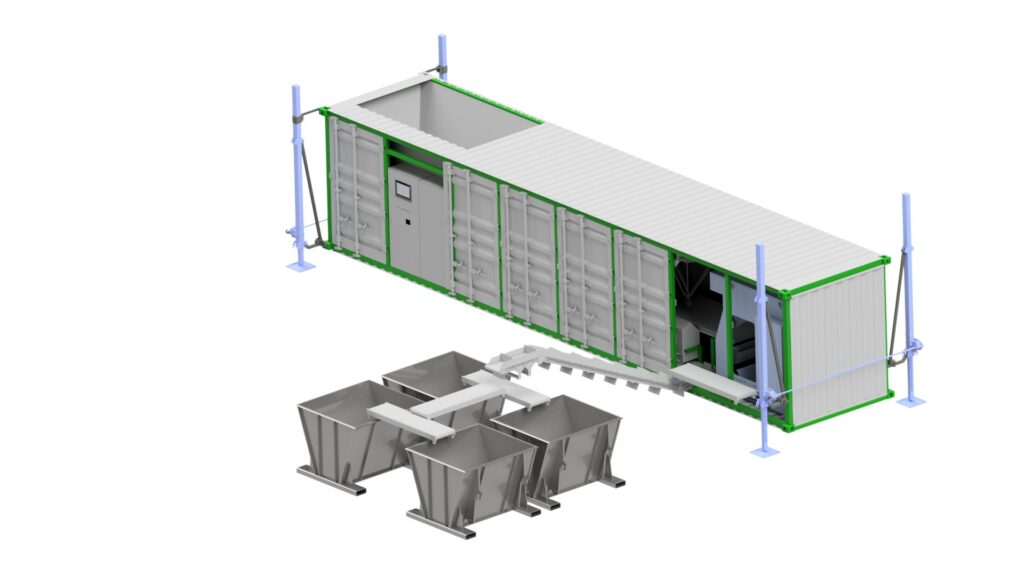
When it comes to our sorting unit, it almost makes one feel sentimental to look back at the beginning. It all started in 2020 with a LinkedIn post from RHI Magnesita asking the community to analyze fired carbon bricks. So, you could say, an open innovation regarding scientific challenges was where it all began. However, LSA accepted this challenge. It took us a while, but after some initial analyses in LSA’s laboratories in Aachen, Germany, we quickly were able to run a pre-test study with RHI employees on site in Germany.
The results were very promising and further cooperation was set. The goal was clear: the development and construction of an automated sorting plant that can be used on a mobile basis. First, rough requirements were defined. The mobile application is a central point as RHI Magnesita also wants to set up the plant at customers` sites in the future to sort on site.
Also, the technical requirements are important. Next to the general throughput and the grain size, the number of different fractions were defined. With these main requirements the development process started. LSA created a first design with the CAD-Software Autodesk Inventor.
To fulfill the basic requirement of mobility, a 40” container was chosen for the base. On the one hand it offers a lot of space and design freedom and on the other hand it is easy to transport. To put some life into the container, LSA created dummies of the necessary components and placed them inside the container. With the first drawing, LSA had a larger meeting with RHI Magnesita to discuss the first draft drawing. All in all, the draft drawing was accepted. Nevertheless, new requirements for the installation site in Austria were identified, that are at some details different to Germany. The main result of the meeting was: We need more space. Therefore, we added a second 40” Container to the design.
The feeding for the plant were set into container 1 and also the parts for the basic supply like compressed air and the dust filter system. The heart of the plant, the actual analyzing and sorting were housed in container 2. Parallel with the design, LSA started to find suppliers for the core components and prepared pre-tests. For example, several buckets full of different bricks were send to a company that builds customized blow-out units. The company tested, if their blow-out units are suitable for bricks and which grain size they can sort.
Further tests have been completed at various points in the project or are still pending. If a supplier company could fulfil the requirements and was convincing, a highly detailed CAD model was created. This detailed model then replaced the dummy in the construction. In this way all dummies were replaced by real representing CAD models and the whole construction got more and more detailed. The development process of such a system naturally requires several iteration loops. Therefore, in bi-weekly meetings with RHI Magnesita the design was discussed and further refined until the final construction. We will present the result of our efforts in one of the next postings.
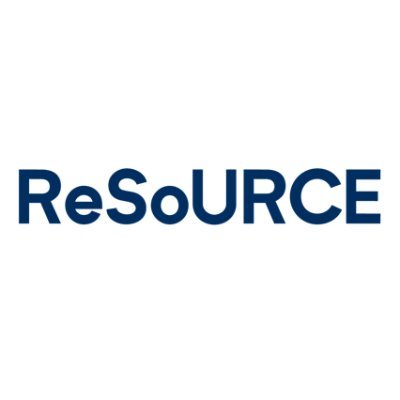
Author’s Portrait
Carsten Coenen
Carsten Coenen is a development engineer at LSA – Laser Analytical Systems & Automation GmbH (Germany). He is working on the mechanical design and the implementation of high-precision 3D-printed parts for use in optical modules. Since 2022 he has been working at LSA. Previously, he completed an apprenticeship as an electronics technician at RWTH Aachen University and received his B.Eng. Mechatronics and M.Sc. Mechatronics from FH Aachen University of Applied Sciences.
During his studies, he already worked as a working student at RWTH Aachen University and at AGVR GmbH (Germany). Since he joined LSA, he has also been involved in EU projects (e.g. REVaMP and ReSoURCE).
Partner
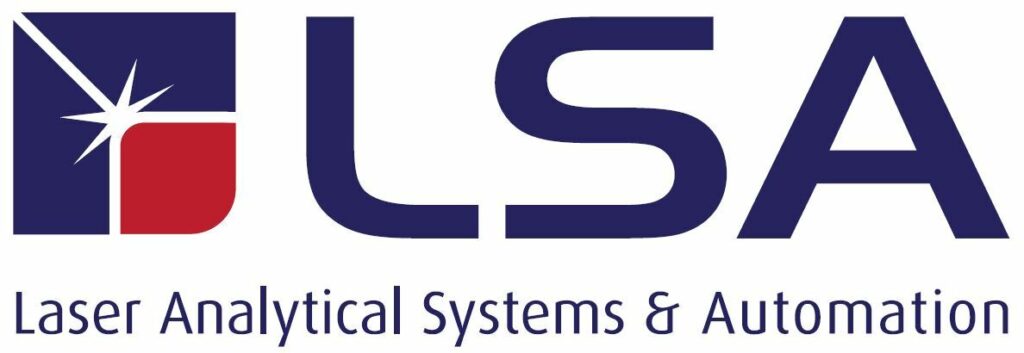