2025 marks the 30th anniversary of the foundation of InnoLas Laser GmbH. Since 1995, the development and manufacturing of highest quality laser sources for scientific and industrial applications made in Germany is the main drive of the company. Through the knowledge and teamwork of the employees, the laser systems produced are customized to the customer’s wishes. Within the first 20 years, the company grew and built laser systems for numerous different applications. For a better separation of the products, the company was split into several companies, each specializing in a different field. At InnoLas Laser, laser sources for scientific applications are the main focus.
InnoLas Laser produces flash lamp and diode pumped laser systems with pulse lengths in the upper picosecond and nanosecond range with pulse energies at 1064nm of a few µJ at 100 kHz to over 7J at 3 Hz and wavelengths of 1064nm to higher harmonic generations as well as OPO capabilities. The products manufactured cover a wide range of specifications needed for the even wider range of application possibilities such as Lidar, Ti-Sa pumping, Thomson scattering, photoacoustic … and in the case of the ReSoURCE project for the recycling of refractive materials.
Furthermore, the availability of technicians and the lifelong support of the laser systems allow the customers to maintain and if needed upgrade their laser systems over the years as specification changes appear in their applications.
InnoLas Laser, with the desire for development of new fields of application, participates in numerous projects in cooperation with international partners. In the case of the ReSoURCE project, to be able to obtain the desired LIBS analysis for sorting of the refractive material, specific changes in the emission output were needed. Through software, hardware and optical optimization the laser system was developed to reach the needed specification.
The headquarter of InnoLas Laser GmbH is located in Krailling near Munich, Germany. The in-house development of the components as well as a tight connection between all departments allows for a smooth planning and manufacturing of the laser systems according to the required specifications.
In 2022, InnoLas Laser GmbH opened another branch office and production facility in Windorf near Passau, Germany. The site was built according to the latest environmental standards and uses geothermal energy for heating and air conditioning. In addition, a high-performance photovoltaic system on the roof ensures a sustainable power supply for the building and the charging of company vehicles.
As founder Reinhard Kelnberger said: “For us a very pleasant working atmosphere is one very important pre-condition for such a well-coordinated and successful development. We are looking forward to more sustainable growth of our company, many new and old satisfied customers, new challenges and especially to improving our products for our costumer’s benefit!”
From 9–12 June 2025, the International Conference on Solid Waste 2025 (ICSWDG2025) has taken place. Hosted by Dongguan University of Technology, Zhejiang University, and the International Waste Working Group (IWWG), the gathering centered around “Waste Management for Carbon Neutrality and Circular Economy”.
The adoption of circular and green economy practices is essential for reducing environmental pollution and mitigating climate change. Despite this, the global economy remains only 7.2% circular, according to the 2024 Circularity Gap Report, highlighting a vast opportunity for progress. ICSWDG2025 offerd a vital platform for scientists, researchers, regional policymakers, and industry professionals to share insights on sustainable waste management, technology, and environmental challenges.
The ReSoURCE project was also presented at ICSWDG2025, contributing to the broader discussion on waste management. The presentation highlighted the project’s overarching objectives, emphasizing its focus on addressing a particularly significant and valuable waste stream within the broader context of sustainable resource management. Key findings from the analysis of the European waste management systems were shared. It concluded with the introduction of a GIS-based map, designed to improve data visualization and decision-making in waste management regarding spent refractories.
Personal notes: It was truly a wonderful and educational experience to participate in an international conference in China. A heartfelt thank you to Prof. Jonathan Wong for warmly welcoming the Austrian participants and taking such excellent care of us. Sincere thanks also to the organizing team for putting together such a well-organized event.
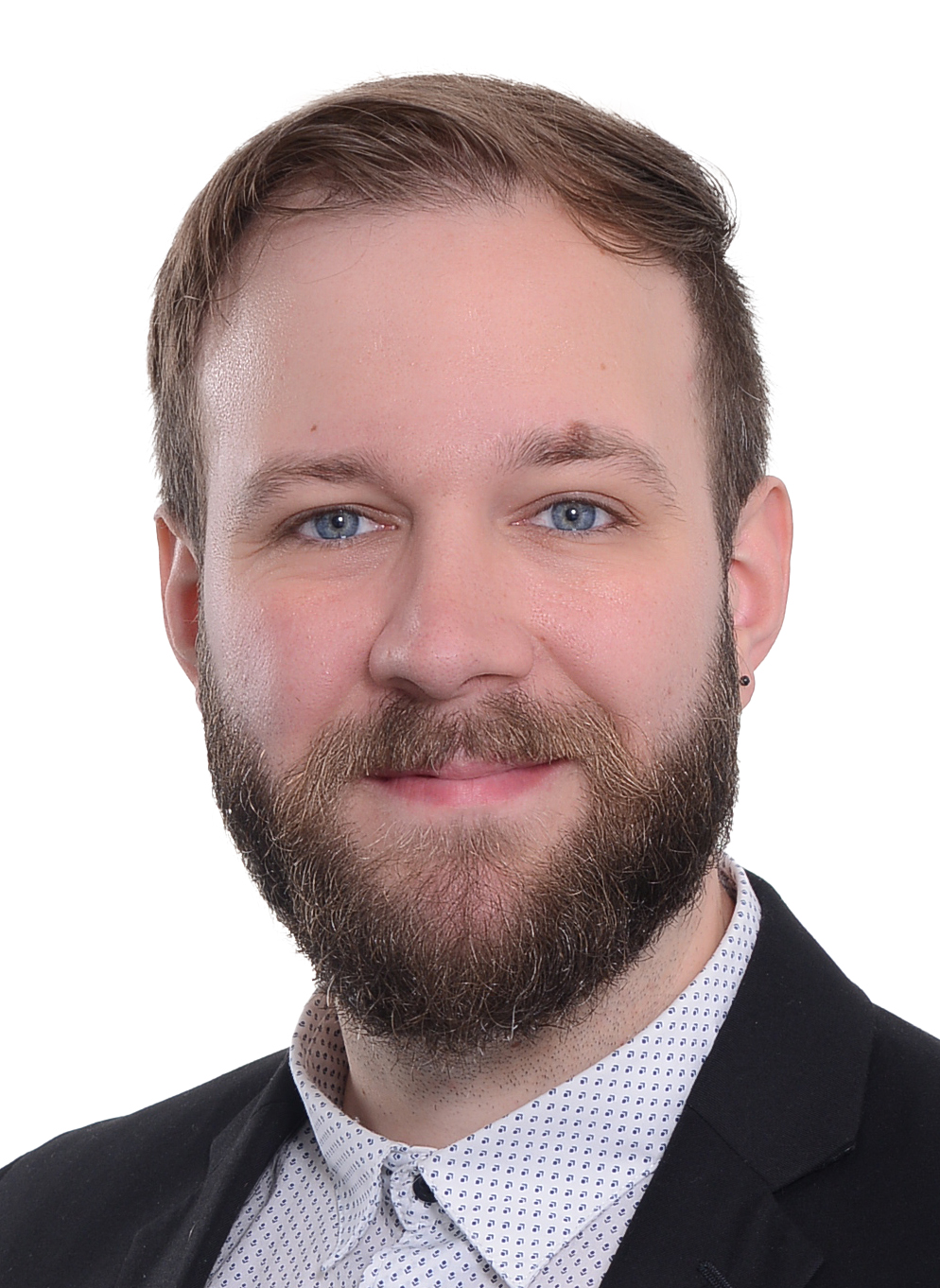
Authors’ Portrait
Florian Feucht
DI Florian Feucht is research associate at the Chair of Waste Management and Waste Treatment at the Montanuniversität Leoben and part of the Workgroup: “Environmental remediation and mineral waste”. Since 2023, he has been enrolled in the university’s PhD Program. He earned his master’s degree in Applied Geoscience from Montanuniversität Leoben, focusing on the chemical-mineralogical characterization of ladle slag. He completed his bachelor’s degree in Earth Sciences at the University of Vienna, with a thesis on the petrological study of mafic and ultramafic rocks. His research interests include the chemical mineralogical characterization of mineral wastes, mineralogy, slag mineralogy, recycling, and waste management.
Three years into the ReSoURCE project, our latest consortium meeting marked a significant milestone: Month 36. This time, we were warmly hosted by CPI at their facilities in the northeast of England, near Newcastle. Upon arrival, CPI colleagues offered a guided tour of their state-of-the-art laboratories and research facilities. Their well-equipped infrastructure provided valuable insight into the technical capacity and innovation potential that CPI brings to the project.
The first day also included smaller group meetings where partners aligned on the progress of various work packages and discussed next steps. The second day was dedicated to a full consortium meeting. With a packed agenda, we reviewed project management updates and heard presentations from all Work Package leaders. These updates focused on both recent progress and the key activities planned for the final phase of the project.
A central focus of the meeting was the discussion around the project’s key exploitable results. Partners engaged in defining which results offer the most relevance and potential impact, as well as how best to maximise their uptake and long-term value. Follow-up meetings are planned to continue aligning on these outcomes, which will be shared in more detail at the ReSoURCE final event. In the evening, the consortium came together for a group dinner—an opportunity to reconnect and strengthen collaboration in a more informal setting.
Before heading home on the third day, we visited the Port of Sunderland. This site stands out for its growing circularity hub, which has spurred the development of a regional industrial cluster. The port plays a vital role in handling commodities such as pulp and general cargo, serving as an intermodal logistics hub with rail connectivity. It also contributes significantly to the local economy.
Our tour, led by the port’s Commercial Manager, began with an overview of Sunderland’s maritime heritage. Once a hub for shipbuilding, the port is now repositioning itself as a centre for green industrial innovation on the northeast coast of England. The circularity hub at the port illustrates the real-world application of circular economy principles and supports broader goals for regional regeneration and decarbonisation. The visit was a compelling example of how industrial reuse and environmental innovation can intersect.
Overall, the M36 gathering was an opportunity to reflect on our journey so far, align on priorities, and reinforce the spirit of collaboration that underpins ReSoURCE. A sincere thank you to our colleagues at CPI for their excellent organisation and hospitality—we truly appreciated the warm welcome and thoughtful planning.
We’re proud of the strong consortium we’ve built and look forward to sharing the outcomes of our work at the ReSoURCE final event. Stay tuned!
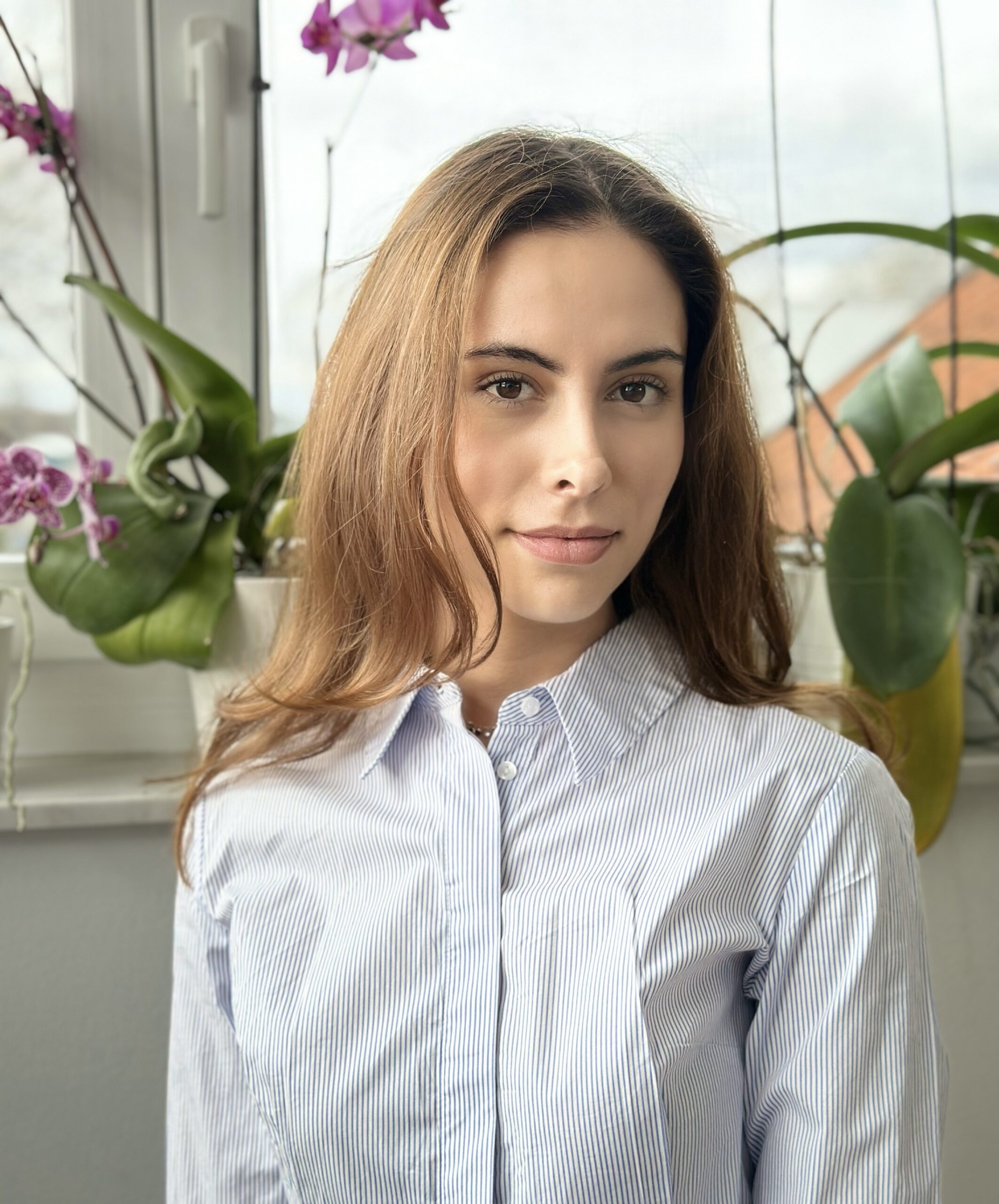
Author’s Portraits
Sofia Iriarte
Sofia is project ReSoURCE´s Science Communicator. She studied Advertising and Public Relations and has a MSc in Communication Science from the University of Vienna. Currently, she is part of the Innovation Management team and Global Communications at RHI Magnesita.
Montanuniversität Leoben, Austria’s leading university for mining, metallurgy, and materials science, has been at the forefront of resource-focused research and education for over 180 years.
Founded in 1840 in Vordernberg as the “Steiermärkisch-Ständische Montanlehranstalt” under the patronage of Archduke Johann of Austria, the institution began its journey under the leadership of metallurgist Peter Tunner. In 1849, it relocated to Leoben, where it gradually evolved into a cornerstone of Austria’s academic landscape. By 1904, the school gained university status as the “Montanistische Hochschule,” granting it the authority to award doctoral degrees and expanding its scientific and research influence.
Throughout the 20th century, Montanuniversität Leoben expanded its academic offerings beyond traditional mining and metallurgy to include fields such as materials science, petroleum engineering, and environmental technology. The 1975 University Organisation Act marked another milestone, officially renaming it Montanuniversität Leoben and solidifying its role within Austria’s higher education system.
Significant investments in infrastructure and innovation followed in the early 2000s, including the establishment of the Raw Materials Center (2006) and the Impulse Centre for Materials (2007). By the 2012/13 academic year, student enrolment had surpassed 3,000, reflecting its growing global reputation.
Today, Montanuniversität Leoben is internationally recognised as a centre of excellence for sustainable raw materials research. Its work spans the entire value chain—from extraction to recycling—with a strong focus on green technologies and circular design. As a proud member of TU Austria, the university plays a critical role in collaborative innovation at the European level.
Within the EU-funded ReSoURCE project, the Chair of Mineral Processing and the Chair of Waste Processing Technology and Waste Management are responsible for developing a comprehensive waste management concept. This includes the chemical and mineralogical characterisation of refractory waste materials, as well as the evaluation of feedstock properties to optimise pre-processing steps for automated sorting. Identifying the most suitable comminution technologies is also a key focus, serving as a foundation for efficient material separation and high-quality recycling outcomes.
The Chair of Mineral Processing at Montanuniversität Leoben focuses on the efficient recovery, separation, and processing of primary and secondary raw materials. Research and teaching emphasize mechanical, physical, and physico-chemical processing methods, particularly for metallic ores, industrial minerals, and recycling materials. Key areas include process and plant engineering, processing characterization, comminution, classification, flotation, magnetic separation, and electrostatic sorting. The chair develops sustainable and resource-efficient technologies along the entire value chain – from the deposit to a marketable product. In addition to laboratory and pilot-scale experiments, numerical simulation methods such as DEM and CFD can also be employed. Collaborations with industrial partners enable practice-oriented research and technology transfer. The aim is to develop viable solutions for environmentally responsible raw material processing and to support the transition to a circular economy.
The Chair of Waste Processing Technology and Waste Management at Montanuniversität Leoben is dedicated to sustainable resource utilisation, the development of innovative recycling technologies and environmental protection. Research priorities include the circular economy, recovery of valuable materials from waste, and the optimisation of waste management systems. The aim is to create ecological and economic solutions for global waste challenges. Through interdisciplinary approaches and close collaboration with industry partners, the chair contributes to a resource-efficient and environmentally friendly future. The chair can be further divided into four specialized working groups, each focusing on distinct topics: Methods and Environmental Analytics, Waste Processing Technology, Future Waste & Waste Management, and Environmental Remediation & Mineral Waste. For instance, the ReSoURCE project, which deals with the mineral composition of refractory materials, is part of the latter. Each group is engaged in national and international projects, providing students with hands-on education and access to cutting-edge research opportunities.
By combining a rich academic heritage with state-of-the-art research, Montanuniversität Leoben continues to lead efforts toward a more sustainable and resource-efficient future.
At the beginning of April, I had the pleasure of joining the Mineral Recycling Forum 2025 in beautiful Cannes, or more precisely, Mandelieu-La Napoule, where the industry met to talk shop about the challenges and opportunities in mineral recycling. And it was far from just another conference.
Together with Lucas Zimmermann from MIRECO, I presented our joint talk “All About Sorting – The Future of Refractory Recycling.” We showed why advanced sorting technology is one of the key levers to unlock higher recycling rates and reduce dependency on primary raw materials and how it can be done in practice.
It was a great opportunity to link our work with ReSoURCE. Presenting this European initiative in front of such a specialized industrial audience felt like an important step to build bridges between innovation, operational reality, and sustainability.
Great Exchange, Great People
What stood out for me? Definitely the quality of discussions and the open, constructive exchange. It’s good to see that in our rather traditional industry, there’s growing momentum around digitalization, circularity, and smarter use of secondary raw materials. Events like this bring together the right people, researchers, plant managers, commercial experts, young professionals, and the mix of perspectives really adds value.
The presentations covered a wide range of topics: from refractory recovery and XRF-based technologies to recycling glass, and strategies to improve raw material circularity. There was a clear red thread throughout: collaboration and innovation are key if we want to scale industrial recycling and move toward a more sustainable raw material supply.
It was also encouraging to see that sorting is increasingly seen as a strategic tool, not just a technical detail. That’s exactly the kind of thinking we need to accelerate change. And it validated the direction we’ve taken with MIRECO and our work on ReSoURCE.
A Quick Thought on Why These Events Matter
Cannes reminded me again how important it is to step out of your day-to-day projects. To listen, to challenge your ideas, and to connect with others who are working on similar issues from different angles. Forums like this give our industry the pulse check it needs and help align around common goals like CO₂ reduction, resource efficiency, and technological progress.
Thanks to the Organizers
Last but not least: a big thank you to Mike O’Driscoll and the IMFORMED team for the professional and smooth organization. You can tell when an event is made by people who know the industry from the inside and who care.
Looking forward to continuing the conversations and to seeing where this growing network leads us next.
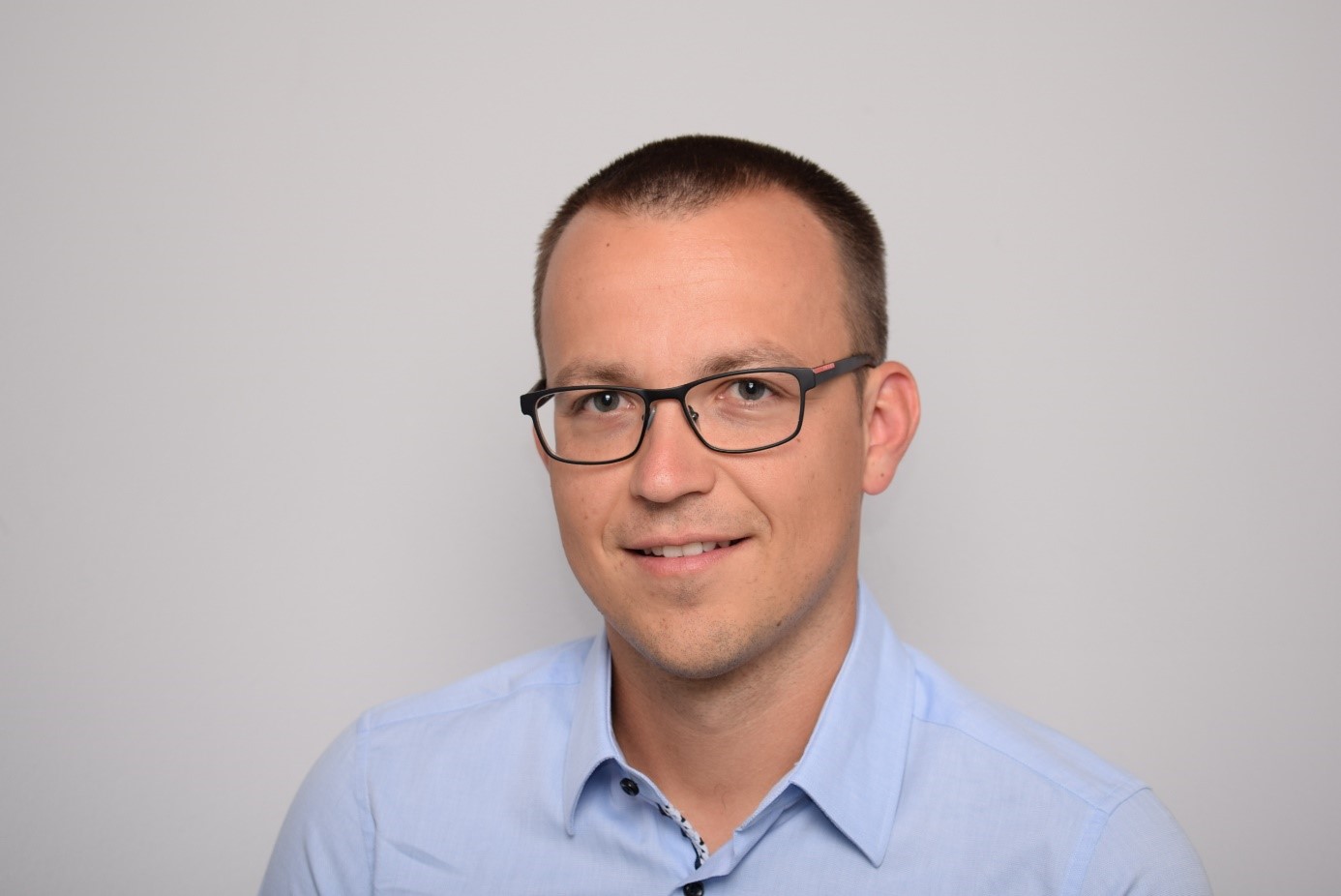
Authors’ Portrait
Alexander Leitner
Alexander studied Material Science at the Montanuniveristät Leoben, focusing on the field of micromechanics and material physics. He joined RHI Magnesita’s Strategic Project and Innovation Team in 2019 and as of early 2025, serves as Head of Pioneer Research at RHI Magnesita.
Recently, I had the opportunity to work on a significant task in Mitterdorf, where I was aiming at integrating Fraunhofer ILT’s software into the Demo A machine. This machine represents the culmination of many months of hard work by ReSoURCE’s project members, and it was highly anticipated by those attending a crucial review meeting at RHI Magnesita’s headquarters in Vienna, most of whom had not seen the machine before and had planned to visit the site after the main gathering.
As I arrived in Mitterdorf, the atmosphere was charged with excitement and a bit of pressure. My primary responsibility was to ensure that our software communicated flawlessly with all of the machine’s sensors and other subsystems. Our software’s task is to combine data from various sensors, including NEO’s hyperspectral cameras, the 3D geometry camera, and Innolas’ LIBS laser. From that we classify the bricks and output sorting decisions to the robots and the air ejection unit. Additionally, I needed to replace a crucial component – the line laser for the 3D geometry system – since the old one had failed just a few days before the review meeting. Replacing the line laser also meant recalibrating the entire 3D geometry system. With the project members in Vienna eager to see the machine in action, I focused on making every moment count.
However, the journey was not without its challenges. Developing the software before my trip to Mitterdorf was particularly demanding. Each line of code I wrote felt like a leap of faith, as I couldn’t test it live until I was on-site. The air ejection unit, in particular, proved to be tricky to control, requiring careful attention and problem-solving.
I was fortunate to have tremendous support from my remote team, which made a significant difference. The collaboration with LSA, who provided both remote and on-site assistance, was invaluable. Their expertise and investment in the project were crucial, especially since they assembled the entire Demo A machine. RHI Magnesita also played a critical role, offering us the facilities and samples we needed to move forward. Before my trip to Mitterdorf, we tried to set up as much as possible, but it was evident that some tests could only be done once I was physically present with the machine.
The machine itself is housed in a temperature-controlled container, which allows it to operate effectively in colder conditions. However, this setup posed another challenge. With some of the machine’s access doors needing to be open to fulfil our tasks, the frigid temperatures caused certain components to refuse operation. We had to strategize our schedule carefully, allowing the machine parts time to warm up for testing.
Finally, after what felt like a never-ending chain of troubleshooting and fine-tuning, we succeeded in getting everything operational just a few hours before the review group arrived. I felt a rush of relief as we tidied up the workspace and prepared our presentation, ensuring that all safety measures were in place, especially since we are dealing with powerful lasers that require careful handling. When the group of visitors arrived, the system operated as intended and we were able to show the individual processes and components to the interested project partners.
While I was busy preparing the machine and missed the review meeting part in Vienna, I was aware that my efforts contributed to the project’s success. It was rewarding to know that I played a part in this significant achievement. This experience taught me valuable lessons about teamwork, time management, and adapting to unexpected challenges. It reinforced the importance of collaboration and preparation in navigating complex projects.
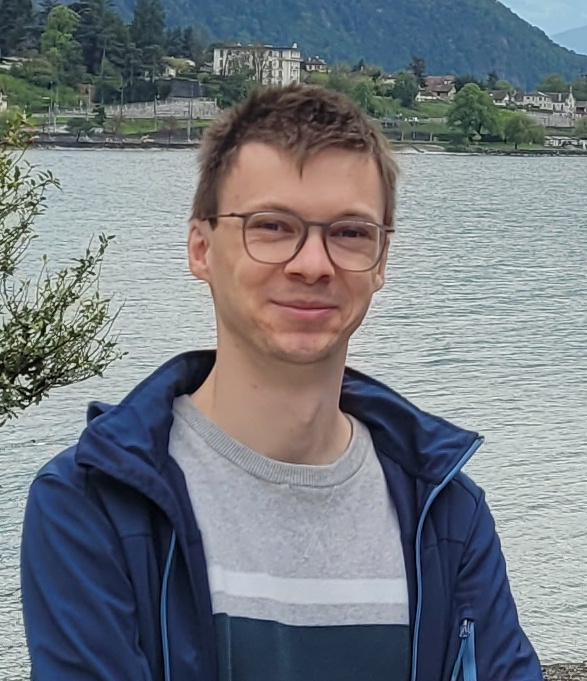
Authors’ Portrait
Yannick Conin
Yannick Conin is a research associate at the Fraunhofer Institute for Laser Technology ILT. He graduated from RWTH University with a master’s degree in mechanical engineering, where he wrote his thesis on sensor fusion for the ReSoURCE project. His research interests include data science, metrology, optics and materials science.
This year’s ReSoURCE project review meeting was hosted in Vienna by RHI Magnesita, marking a significant milestone for our consortium. For many of our partners, as well as our project officer and the technical expert, it was the first time visiting our facilities in our headquarters.
The two-day meeting began on Tuesday morning with a full agenda. Each partner leading a work package had the opportunity to present the progress of their respective work packages with the support of all the other partners involved while fostering valuable discussions and knowledge exchange. We concluded the day with a networking dinner, where we enjoyed delicious Austrian cuisine- a perfect setting for informal discussions and strengthening collaborations.
The highlight of the visit – and the entire review meeting – was seeing the RAPTOR in action. While many of us had previously seen images of the cutting-edge automated sorting machine, witnessing it operate in real life was an entirely different experience. Our colleagues from LSA and RHI Magnesita guided us through the machine’s interior, explaining each station in detail and demonstrating the LIBS (Laser-Induced Breakdown Spectroscopy) technology in action. NEO and ILT could present their related work regarding HSI (hyperspectral imaging) and integration of the multi-sensor setup.
The visit was undoubtedly a key moment of our meeting, sparking engaging discussions and reinforcing the importance of innovation in refractory recycling. The entire gathering was filled with knowledge sharing, hands-on experiences, and valuable exchanges – making a truly successful event for the ReSoURCE project.
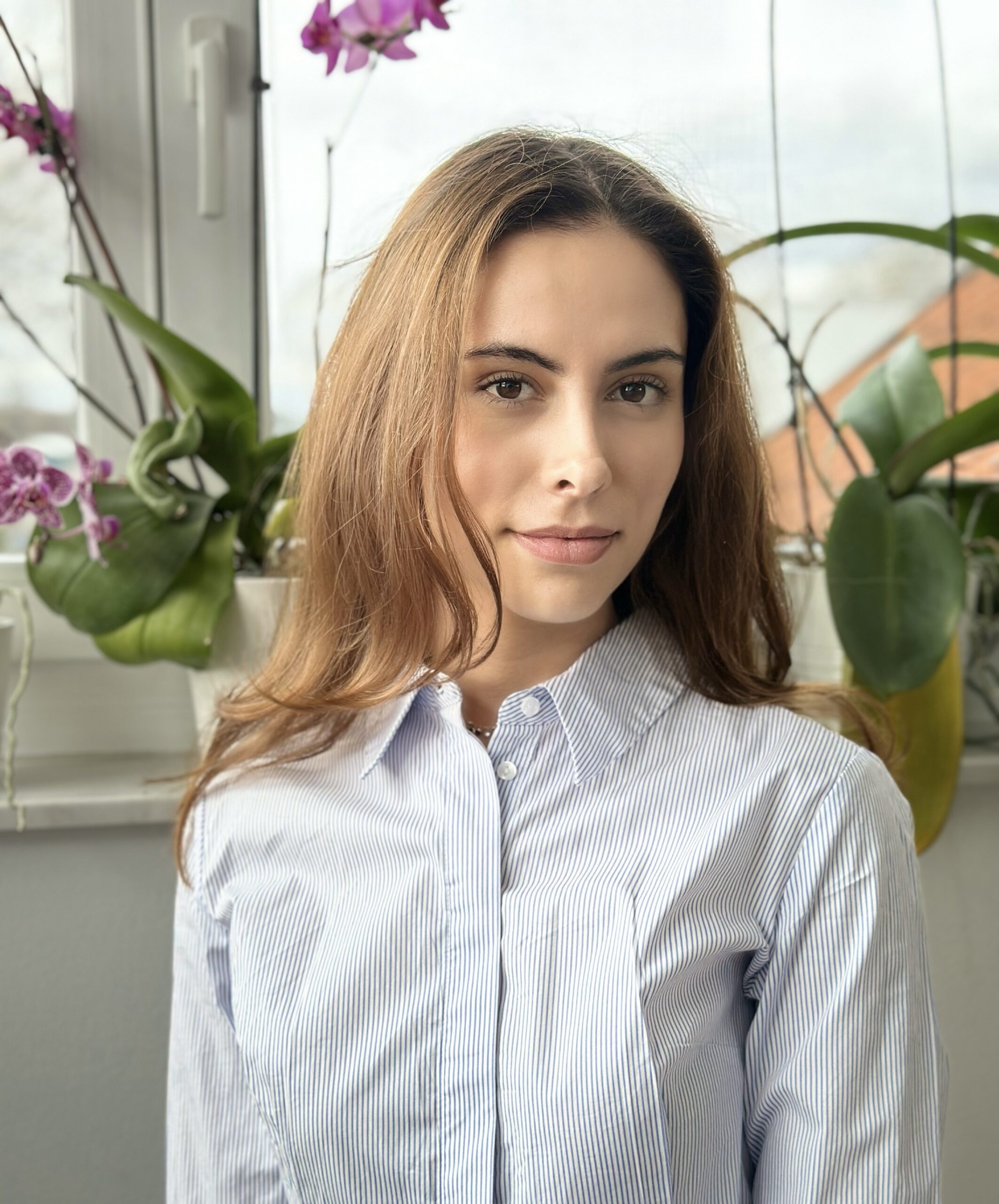
Author’s Portraits
Sofia Iriarte
Sofia is project ReSoURCE´s Science Communicator. She studied Advertising and Public Relations and has a MSc in Communication Science from the University of Vienna. Currently, she is part of the Innovation Management team and Global Communications at RHI Magnesita.
After completing the one-year mechanical assembly phase of the ReSoURCE sorting system Demo A (a.k.a the Raptor), we are proud to announce that the plant has successfully completed its 1,000 km journey and has now arrived at its new home at RHI Magnesita- Mireco in Mitterdorf (St. Barbara im Mürztal), Austria.
We are pleased with the smooth transport process and the efficient assembly on-site, which reflects the meticulous planning and coordination of the past weeks. The entire system was transported using three trucks: two trucks carried one container each, along with the connecting bridge, while a third truck transported smaller components, and the tools required for assembly.
At its destination in the picturesque Mürztal region, the two containers and the connecting module were unloaded sequentially using a 100-ton crane. Subsequently, assembly work began on the individual components, which had been packed for transport. Among others, these included the material intake hopper mounted on Container 1, the external piping for the air extraction and filtration system, and the conveyor belt located between the containers. This was specifically designed to fold for transport and therefore was unfolded and installed during the assembly process.
The essential assembly of the 36-ton sorting system, housed in two 40-foot shipping containers, was completed within just one workweek. We extend our gratitude to RHI Magnesita for their thorough preparation of the installation site and for actively supporting our engineers and technicians from LSA GmbH on-site. The system has successfully passed its first validation, handling wind, weather, and the harsh temperatures of the Austrian winter without issue.
The current focus is on the training of future RHI Magnesita’s operating personnel, as well as further fine-tuning of the software. Our experts are on-site to provide comprehensive guidance on process workflows and system operation, ensuring the plant is ready to begin its new chapter in Austria.
We are looking forward to utilizing the insights gained during the commissioning phase in Austria to further optimize the system and refine its processes across all modules. The successful transport and installation of the plant mark an important step towards the sustainable and economically efficient reuse of recycled refractory materials.
Together with RHI Magnesita and our project partners, we are excited to drive the future of recycling to the next level!
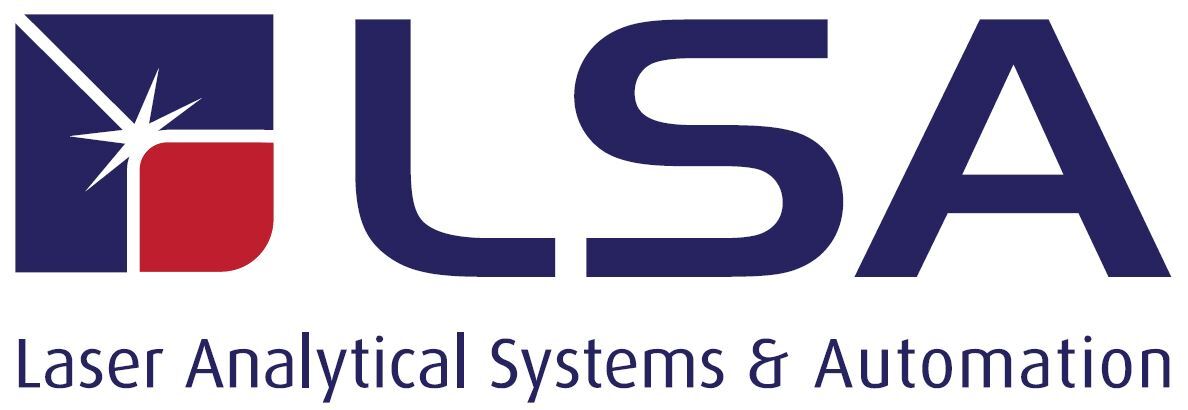
Author’s Portraits
Volker Mörkens
From 13 – 15 November, the largest German-speaking waste management conference in Europe was held at the Montanuniversitaet Leoben. The event was organised by the Chair of Waste Processing Technology and Waste Management at the Montanuniversitaet Leoben and takes place every two years at the beginning of November. This prestigious gathering brought together participants from academia and industry to discuss cutting-edge topics in waste management and technology. The 2024 conference focused on key areas such as circular economy, sensor-based sorting including robotics, artificial intelligence, and eco-design. Other highlights included case studies, best practices, and discussions on mineral waste, industrial residues, and climate protection. A total of 752 attendees enjoyed 163 presentations organized into five parallel sessions over the course of the three-day event.
Of course, our ReSoURCE project was also represented and was already mentioned on the first day in the plenary lecture by Univ.-Prof. Dipl.-Ing. Dr.mont. Roland Pomberger. On Thursday evening, the project was featured in a detailed presentation titled “The heat is on!” which discussed the journey from material characterization to sensor training based on insights obtained during the project. Additionally, on the final day, participants learned about the practical applications of the lasers developed by LSA, with a focus on the sorting unit created as part of the ReSoURCE initiative.
Picture 1: Alexander Leitner and Florian Feucht presenting project ReSoURCE.
I would like to take this opportunity to thank Alexander Leitner and Simone Neuhold once again: I really enjoyed working with you on the presentation as well as presenting it together.
One of the most anticipated sessions of the conference is the ‘Leoben Waste Debate’, where a specific topic sparks lively discussion among experts. This year, the debate centered on the question, “Secondary raw materials need rights: Are end-of-waste regulations THE solution for an intelligent circular economy?” This engaging one-hour discussion took place at the end of the first day, providing a thought-provoking conclusion to the first day.
Picture 2: Leoben Waste Debate
Three conference days full of exciting presentations later, I can summarise the Recy DepoTech 2024 as a very successful event, both as a visitor and as part of the organisation team.
Will visit again, so see you at Recy DepoTech 2026!
Picture 3: Organization Team behind Recy DepoTech
Photo credits: © Chair of Waste Processing Technology and Waste Management of Montanuniversitaet Leoben.
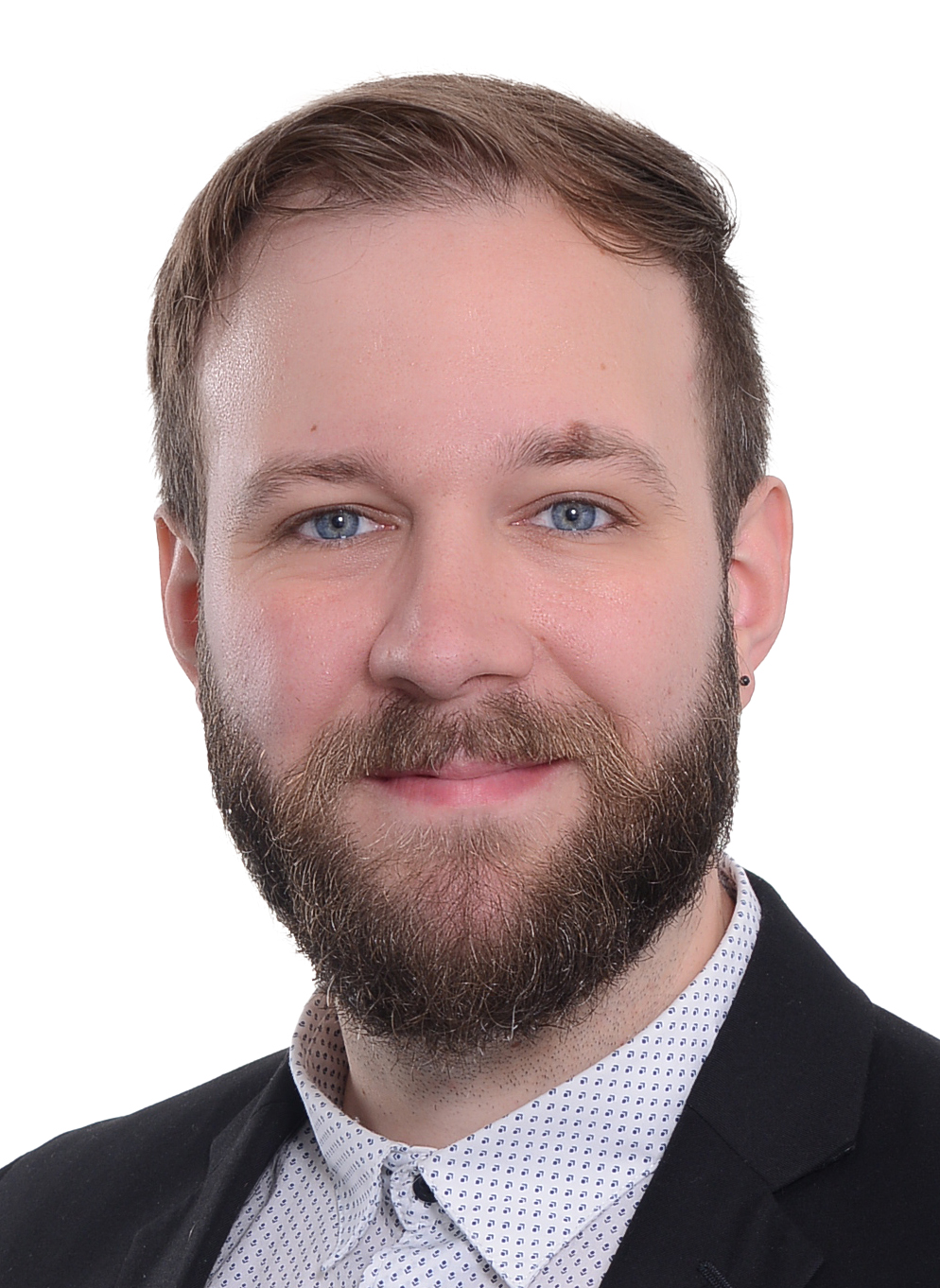
Authors’ Portrait
Florian Feucht
DI Florian Feucht is research associate at the Chair of Waste Management and Waste Treatment at the Montanuniversität Leoben and part of the Workgroup: “Environmental remediation and mineral waste”. Since 2023, he has been enrolled in the university’s PhD Program. He earned his master’s degree in Applied Geoscience from Montanuniversität Leoben, focusing on the chemical-mineralogical characterization of ladle slag. He completed his bachelor’s degree in Earth Sciences at the University of Vienna, with a thesis on the petrological study of mafic and ultramafic rocks. His research interests include the chemical mineralogical characterization of mineral wastes, mineralogy, slag mineralogy, recycling, and waste management.
One year ago, in October 2023, our project partner NEO installed a Hyper Spectral Imaging (HSI) system in Leoben and provided us with training to generate a substantial dataset—a quite large dataset of over 150 GB—aimed at developing a classification model to support LIBS measurements for sorting our spent refractories.
This HSI system consists of a high resolution optical sensor operating in the 400-2500 nm range. It can be used to detect and differentiate materials based on their unique spectral signatures, which are influenced by mineralogy and bonding systems. The HSI sensor supports the LIBS unit in two primary ways:
- Identifying Key Regions: It locates areas on the sample that are significant for classification, such as regions that are free from contamination.
- Material Classification: It classifies spent refractories, thereby improving accuracy and validating classification decisions.
To achieve effective classification, the system must be trained using samples with known properties, referred to as ground truth data. This data serves as a benchmark for training multivariate and machine learning models. In the context of optical sensors, these samples are typically prepared under controlled conditions, ensuring that their spectral properties are well-documented and reliably reproducible. Ground truth data is crucial for training algorithms, as it provides a reference for the model to learn how to recognize patterns. However, as you might recall from previous blog posts, determining the exact material properties of spent refractories poses certain challenges. Fortunately, we recognized the importance of sampling early in the project and gained valuable insights into our feedstock, enabling us to provide well-characterized samples for our initial training.
For our sample preparation, we selected spent refractory samples from various customers and aggregates corresponding to specific sorting classes including defined common contaminants. We identified these classes either visually through well-known optical features or by chemically analyzing the bricks for confirmation. We then manually crushed the samples to ensure their integrity, ultimately providing images and data for about 2,000 pieces representing the sample shape to be placed on the conveyor belt in the sorting equipment.
Once prepared, these samples were analyzed using HSI. For data acquisition, each sample was illuminated, and the resulting spectral data was recorded as a reflectance spectrum. Consistency in data collection and meticulous documentation was crucial, so in total, we stored the aforementioned 150 GB of spectral data, along with an additional 4.5 GB of images documenting the sample origins, setup, and measurement settings.
After gathering the spectral data, we shared it with NEO to extract relevant features for classification. This process may involve statistical analyses or dimensionality reduction techniques, such as Principal Component Analysis (PCA), to pinpoint the most informative aspects of the spectral data. To aid in this, we also provided spectral data for our most common raw materials, helping to link spectral features to material classifications.
With the ground truth data and extracted features, we began the actual model training. By applying machine learning algorithms, such as Support Vector Machines (SVM), the model learns to associate specific spectral patterns with their corresponding material classifications. The final step involves validating and testing the model to ensure its effectiveness. This validation process requires a separate set of samples not included in the training phase, which assesses the model’s ability to generalize to new, unseen data—an essential measure of its practical applicability.
A year after the installation of the equipment and continuous exchange with NEO, we are pleased to report that we can classify certain sorting classes with an accuracy exceeding 95%. While fine-tuning remains necessary and the upscaling to actual equipment is still in progress, we are excited about the advancements made in our material classification capabilities. By focusing on chemical and mineralogical properties rather than visual features, we are not only minimizing subjectivity in our sorting process but we are also able to customize our sorting classes to further valorize our circular raw materials.
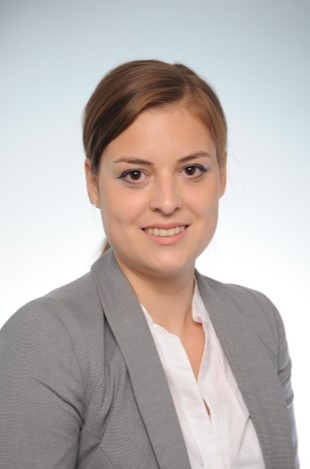
Authors Portraits
Simone Neuhold
Dr. Simone Neuhold currently works for RHI Magnesita. Before she joined the company she was hired at Pilkington Deutschland AG/NSG Group. Simone studied at the TU Graz Chemistry and Advanced Materials Science, and at the Montanuniveristaet Leoben Waste Management and Waste Processing Technologies. Her research interests are recycling of mineral wastes, materials science and oekodesign.
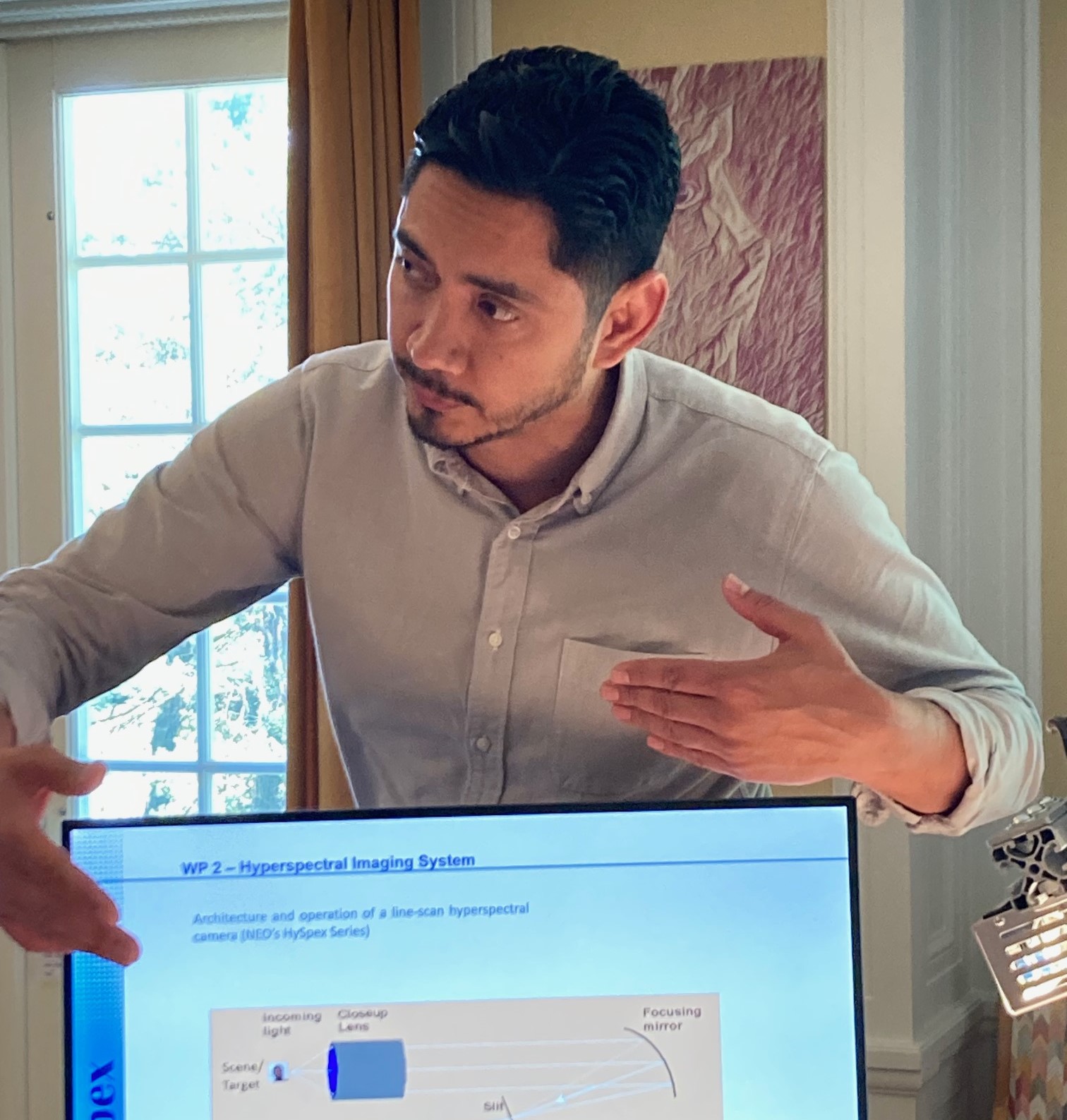
Julio Hernandez
Julio Hernandez, MSc, is a senior research scientist at Norsk Elektro Optikk AS with over 15 years of experience in the field of hyperspectral imaging. Julio has worked developing scientific-grade hyperspectral cameras and data acquisition systems for a variety of applications within remote sensing, defense, industry and biomedical research. He is currently Manager of the Hyperspectral Applications department at HySpex, focused on developing customized solutions for end-users and promoting the adoption of hyperspectral technologies in new markets. Julio studied Physics at the Autonomous National University of Mexico (Mexico) and Nanotechnology at Chalmers University of Technology (Sweden) with specialization in quantum information systems.